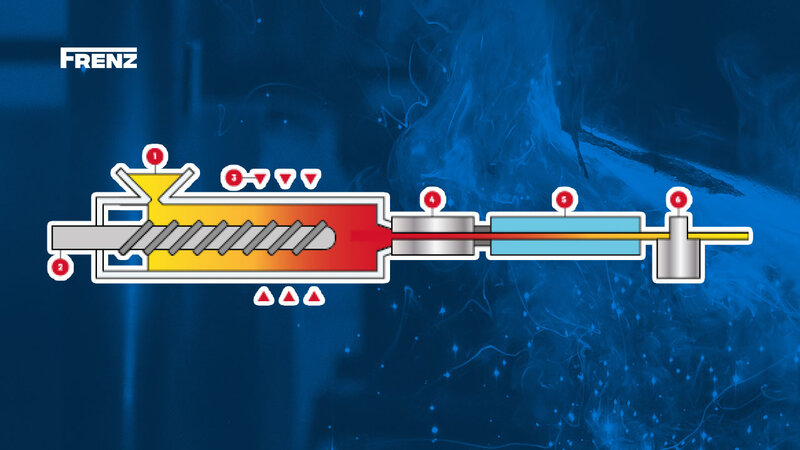
Alles über Extrudieren und den Extrusionsprozess
Erfahre alles über den Extrusionsprozess, Techniken und Tipps für eine effiziente Kunststoffproduktion.
Was ist Extrusion?
Kunststoffextrusion ist ein kontinuierlicher oder diskontinuierlicher Prozess, bei dem der Kunststoff in einer Schnecke plastifiziert und mit den erforderlichen Additiven vermischt wird, um bestimmte Materialeigenschaften zu erzielen. Der Prozess ist kontinuierlich bei der Herstellung von beispielsweise Rohren und diskontinuierlich bei der Herstellung von beispielsweise PET-Flaschen. Unter hohem Druck wird der Kunststoff durch eine Matrize gepresst, wodurch ein Produkt entsteht, wie zum Beispiel ein Rohr, ein Profil, ein Kabel usw.
Die Extrusion von Kunststoffprodukten in 6 Schritten
-
Trocknung und Transport des Kunststoffgranulats
Falls erforderlich, wird das Kunststoffgranulat zunächst getrocknet und anschließend zur Extruderanlage transportiert. Oft werden Additive wie Farbstoffe beigemischt. -
Einspeisung des Granulats
Das Granulat wird in die Schnecke des Extruders eingeführt. -
Mischen und Transportieren
Das Kunststoffmaterial wird in der Schnecke gemischt und zur Spitze der Schnecke transportiert. -
Plastifizierung des Granulats
Das Granulat wird durch Heizung und Reibung in der Schnecke aufgeschmolzen. Hier wird in der regel heizbänder verwendet -
Pressen durch die Matrize
Das plastifizierte Material wird unter hohem Druck durch eine Matrize gepresst, wodurch die gewünschte Form entsteht. -
Aushärtung und Längenanpassung
Nach dem Austritt aus der Matrize wird das Material durch Umgebungs- oder Kühlwasser abgekühlt und anschließend auf die gewünschte Länge zugeschnitten.
Der Extruder
Der Extruder besteht aus den folgenden Teilen:
Plastifizierung
Dieser Abschnitt umfasst die Schnecke und den Zylinder, in dem sich die Schnecke befindet.
- Die Schnecke: Sie schmilzt das Kunststoffgranulat und mischt die Additive in diese Schmelze ein.
- Funktionsweise: Dies geschieht durch elektrische Beheizung des Zylinders und die Reibung in der Schnecke.
- Druckaufbau: Der Kunststoff wird durch den in der Schnecke erzeugten Druck oder durch den konstanten Druck einer Schmelzepumpe durch die Matrize gepresst.
Matrize
In der Matrize wird der Kunststoff (kontinuierlich) in die gewünschte Produktform gebracht. Je nach Produkt werden verschiedene Extrusionstechniken angewendet. Nach dem Austritt aus der Matrize wird das Produkt abgekühlt.
Der Extruder ist somit eine Schlüsselkomponente im Extrusionsprozess, da er sowohl die Schmelze erzeugt als auch die Grundlage für die Formgebung schafft.
Die Extrusionsmatrize
Die Extrusionsmatrize spielt eine zentrale Rolle im Extrusionsprozess. Die „Qualität“ der Matrize hat einen erheblichen Einfluss auf die Qualität des Endprodukts sowie auf die Effizienz des Extruders.
Beispiele für Matrizen
-
Links: Eine Extrusionsmatrize, die in einem kontinuierlichen Prozess verwendet wird. Solche Matrizen kommen z. B. bei der Herstellung von Rohren, Profilen oder Kabeln zum Einsatz.
-
Rechts: Eine Blasextrusionsmatrize, die in diskontinuierlichen Prozessen verwendet wird, wie z. B. bei der Herstellung von Kunststoff-PET-Flaschen.
Bedeutung der Temperaturkontrolle
Die Temperaturregelung ist ein entscheidender Faktor im Extrusionsprozess. Sowohl der Zylinder als auch die Schnecke müssen auf eine materialabhängige Temperatur gebracht werden, um den Prozess zu starten. Die Zylindertemperatur variiert dabei je nach Zone, da in der Schnecke verschiedene Prozesse ablaufen
Zonale Prozesse in der Schnecke
-
Einführung des Kunststoffgranulats
Hier wird das Granulat in den Extruder eingespeist. -
Plastifizierung des Kunststoffgranulats
Das Granulat wird durch Wärme und Reibung aufgeschmolzen. -
Mischen der Additive
Die Additive werden gleichmäßig in die Kunststoffschmelze integriert. -
Entgasung (bei bestimmten Kunststoffen)
In einigen Fällen wird Gas aus der Schmelze entfernt, um die Produktqualität zu verbessern. -
Komprimierung des Kunststoffs
Die Schmelze wird verdichtet, bevor sie durch die Matrize gepresst wird.
Wichtigkeit der konstanten Temperatur
- Der Zylinder muss während des gesamten Prozesses die optimalen Temperaturen halten, um eine effiziente Verarbeitung des Kunststoffs zu gewährleisten.
- Eine konstante Temperatur und ein gleichmäßiger Druck sind essenziell, um die Qualität des Endprodukts sicherzustellen und eine hohe Produktionsausbeute zu erzielen.
Temperaturkontrolle nach der Matrize
Bei verschiedenen Extrusionstechniken ist es auch wichtig, die Temperatur des Produkts zu kontrollieren, wenn es die Matrize verlässt und zu einem Endprodukt weiterverarbeitet wird:
- Bei der Extrusion von Profilen müssen diese häufig in Wasserbädern gekühlt werden, um sie auf die richtige Temperatur zu bringen, damit sie zugeschnitten und verpackt werden können.
- Bei der Extrusion von Folien und Plattenmaterialien wird der Kunststoff nach dem Austritt aus der Matrize über Walzen geführt, um die Temperatur zu halten oder ihn kontrolliert abzukühlen.
Was kann schiefgehen
-
Überhitzung des Kunststoffs beim Einzug in die Schnecke
- Wenn der Kunststoff bereits zu warm ist, bevor er in die Schnecke eingeführt wird, plastifiziert er zu früh. Dies kann dazu führen, dass er nicht mehr oder nicht schnell genug in die Schnecke transportiert werden kann.
- Lösung: Die Kühlung der Einzugszone ist oft notwendig, um einen schnellen und reibungslosen Einzug sicherzustellen.
-
Zu niedrige Temperatur im Zylinder
- Wenn die Zylindertemperatur zu niedrig ist, wird der Kunststoff nicht ausreichend plastifiziert. Dies kann dazu führen, dass der Kunststoff nicht homogen mit den Additiven gemischt wird, wodurch das Endprodukt nicht die gewünschte Qualität erreicht.
- Wenn die Zylindertemperatur zu niedrig ist, wird der Kunststoff nicht ausreichend plastifiziert. Dies kann dazu führen, dass der Kunststoff nicht homogen mit den Additiven gemischt wird, wodurch das Endprodukt nicht die gewünschte Qualität erreicht.
-
Überhitzung des Kunststoffs im Zylinder
- Wird der Kunststoff im Zylinder zu heiß, kann er verbrennen, was zu unerwünschten Änderungen in seinen Eigenschaften führt.
- Lösung: Der Zylinder muss auf die richtigen Verarbeitungstemperaturen eingestellt und konstant gehalten werden, um die Qualität des Endprodukts zu sichern und eine maximale Produktionsleistung zu erreichen.
-
Temperaturschwankungen bei Walzenrollen
- Wenn die Walzenrollen nicht konstant auf der erforderlichen Temperatur gehalten werden oder die Temperatur über die Länge der Walze zu stark variiert, kann dies zu Problemen führen.
- Mögliche Ursachen:
- Das Temperiergerät liefert nicht genügend Heiz- oder Kühlkapazität.
- Die Pumpenkapazität ist zu niedrig, sodass Wasser oder Öl nicht schnell genug durch die Walzenrollen strömt.
- Folge: Die Temperatur der Walze bleibt nicht konstant, was die Qualität des Endprodukts beeinträchtigt.
Das Extrusionsverfahren verbessern
Um den Prozess zu verbessern, muss die richtige Methode zum Heizen und Kühlen gewählt werden.
- Die Kühlung der Einzugszone wird oft mit Wasser aus dem zentralen Kühlsystem durchgeführt, wodurch die Temperatur nicht eingestellt werden kann, sondern von dem verfügbaren Kühlwasser abhängt. Dies führt in vielen Fällen zu Korrosion, und das Kühlsystem kann im Laufe der Zeit verstopfen, wodurch die Kühlkapazität verringert wird.
- Das Erwärmen des Zylinders erfolgt in den meisten Fällen mit elektrischen Heizelementen. In einigen Fällen wird auf die Erwärmung mit Wasser (unter Druck) oder Öl (für höhere Temperaturen) zurückgegriffen. Sehr wichtig ist eine genaue Messung der Temperatur pro Zone, da dieser Wert für das Erhitzen oder Kühlen des Zylinders verwendet wird. Wenn diese Messung nicht korrekt ist, kann der Prozess nicht gut gesteuert werden. Es ist auch wichtig, regelmäßig zu überprüfen, ob die Heizelemente noch einwandfrei funktionieren, da diese durch Alterung oder fehlerhafte Montage durchbrennen können.
- Bei einigen Kunststoffen muss im Prozess neben dem Erwärmen (insbesondere beim Start des Prozesses) auch die Wärme abgeführt werden, die durch die Reibung des Kunststoffs in der Schnecke/zylinder entsteht. Hierfür wird Kühlung durch Wasser oder Luft angewendet, wobei Wasser in den meisten Fällen eine höhere Kühlkapazität bietet. Der Nachteil der Wasser-Kühlung ist die Entstehung von Korrosion und Verkalkung der Leitungen, was zu Verstopfungen und einer verringerten Kühlkapazität führt.
- Durch den Einsatz von Temperiergeräten mit thermischer Öl kann mit externem Kühlwasser auch das thermische Öl und damit der Prozess gekühlt werden. Auf diese Weise kann eine hohe Kühl- und Heizkapazität erreicht werden. Der Nachteil von thermischem Öl ist die hohe Temperatur der verschiedenen Schläuche und die Gefahr von Leckagen, wenn die Verbindungen nicht richtig angeschlossen sind. Auch altert das Öl im Laufe der Zeit und muss dann ersetzt werden. Der Vorteil ist jedoch, dass keine Probleme mit Korrosion und Verkalkung auftreten können.
Extrusionstechniken
- Folienextrusion
- Plattenextrusion
- Profilextrusion
- Blasformextrusion
- Compoundieren